Impact of updated Building Regulations on Sustainable Building Practices;
- SPD Studio
- Apr 17, 2023
- 3 min read
Ventilation, Thermal Efficiency, Overheating, and EV Charging.
The construction industry has a huge role in reducing carbon emissions. According to the UK Green Building Council, the UK-built environment (buildings and infrastructure) is responsible for 25% of UK greenhouse gas emissions. And a recent United Nations report shows the global building industry alone contributes 38 per cent of total global emissions. (More on this ,can be found HERE)
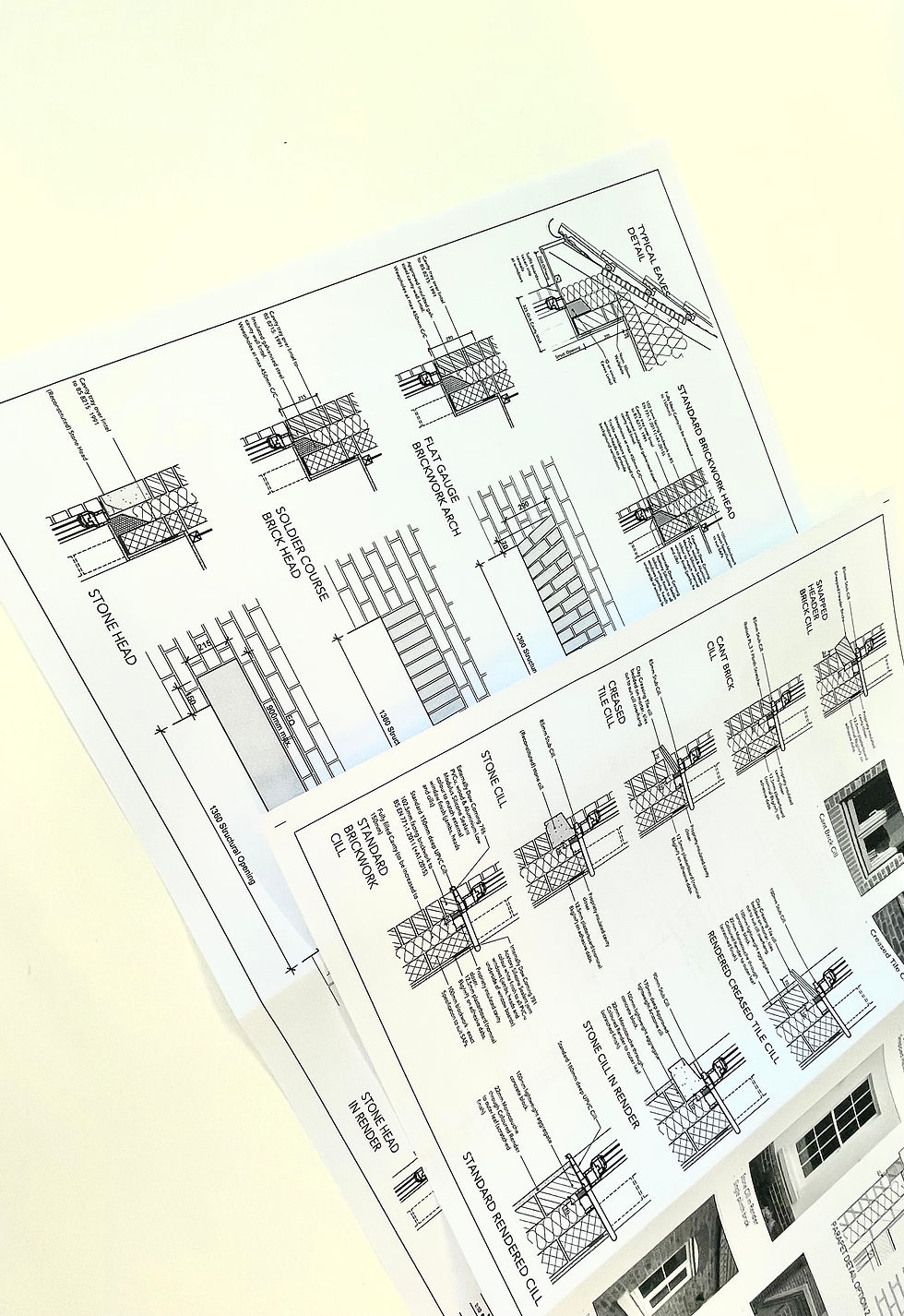
In response, the UK Government introduced The Climate Change Act 2008 to reduce emissions and slow the effect of climate change. It set a statutory target to reduce UK Greenhouse Gas (GHG) Emissions by at least 80 per cent (against 1990 levels) by 2050. Then in June 2019, secondary legislation was passed that extended that target to "at least 100 per cent". Simply put, if this audacious target is met, the UK will stop contributing to global emissions by 2050.
As part of the Construction Industry's efforts to contribute towards emission reductions, all projects registered/notified to Local Authority Building Control bodies since June 2022 (subject to specific date-related caveats which are now superseded) are now subject to the more stringent requirements of the Regulations, including updated Approved Documents F (ventilation), L (thermal efficiency), O (overheating) and S (EV charging). We should be mindful that the provisions for increased thermal efficiencies, etc., apply to new build projects and individual dwelling refurbishments and extension projects.

Developers must factor in increased build cost rates/percentages for all developments to ensure they provide suitable, feasible returns. A summary of changes that any individual commissioning their new build dwelling must be aware of is shown below. These are all new and enhanced elements of build specification which are 'in addition to/over and above' what would typically have been required before June 2022 when the old regulations applied.
Approximately 25 - 50% increase in 'typical' external fabric insulation thicknesses depending upon external fabric element and actual insulant product specification. A basic example of this is where an external brick cavity wall will now need an additional 50mm of mineral fibre full-fill insulation in addition to the previous 100mm required is now increasing the structural width to 350mm, plus internal finishes,
Using Air Source Heat Pumps (ASHPs) instead of gas boiler central heating systems to achieve compliance will typically be the 'default' option to assist with Part L compliance,
Increased reliance upon Solar PV panel installations (be it as part of the roofscape of individual dwellings or communal-based localised 'Energy Centres' – built as part of new smaller scale developments, where renewables are harvested for collaborative usage and distribution,
MHVR (Mechanical Heat + Ventilation Recovery) systems are a typical specification necessity instead of previously using basic background/trickle ventilation methods to achieve compliance,
Glazing percentage areas – relative to dwelling facade orientations and room areas- need further design considerations and assessment from a very early stage of any dwelling design concept, especially for more 'bespoke' or contemporary design approach dwellings. As part of this, a key consideration would likely be an evaluation of 'design aspiration vs achieving compliance vs build cost implications'. i.e. the glazing module specifications (especially designs with significant glazed elements) would be a key specification item with possible associated cost implications,
The increased utilisation of waste hot water heat recovery systems - which would have increased design / detailing considerations in conjunction with cost implications also,
The possible need for dwellings to achieve improved results when Air Pressure tested. Improving the previous default values may help achieve compliance in conjunction with other measures noted.
In addition to increasing construction costs, one of the most important factors to consider is that it has now become vital that the services of a specialist energy / SAP Assessor be engaged at the early stages of any project to assist with the overall design process to help both the client/developer and design team to establish the most means effective way of compliance relative to the merits of each house design. This process applies, regardless of a commission being a one-off bespoke dwelling – or indeed a developer-led development running into several hundreds of properties – close to the site context and unique micro-climate if or as applicable.

Here at SPD Studio, we offer sustainability and technical advice and assistance on any project type to ensure that all aspects of the Building Regulations are met whilst incorporating any specific client requirements – established as part of the 'briefing' process - concerning materials, construction principles and any precise/requisite M&E (mechanical and electrical) requirements. Whether you are a developer or an individual seeking to build a custom property, SPD can provide expert service and guidance on design considerations related to regulations. We work with Accredited Energy Assessors to help establish your goals, agree on project requirements, and produce detailed construction drawing packages and associated build / product specifications.
Author- Tim Wright, Senior Architectural Technician
Comments